The Art and Science of TIG Welding: Techniques, Tools, and Tips
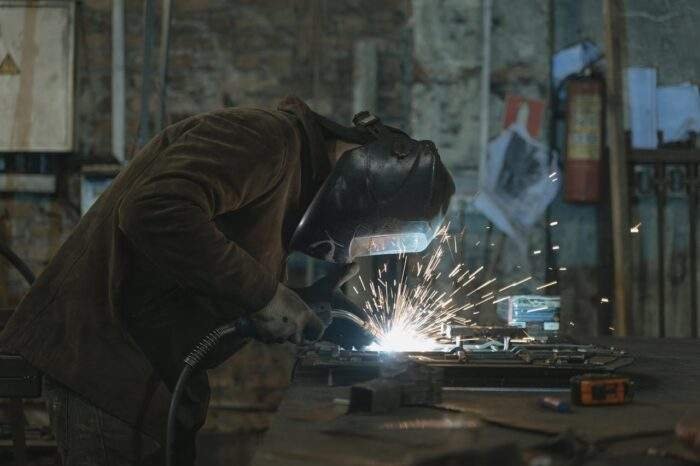
Table of Contents
- Introduction to TIG Welding
- Essential Tools for TIG Welding
- Mastering TIG Welding Techniques
- Common Challenges and Solutions in TIG Welding
- Safety Protocols for TIG Welding
- The Benefits of TIG Welding for Various Industries
- Conclusion
Introduction to TIG Welding
TIG welding, or Tungsten Inert Gas welding, is heralded for its precision and versatility. Unlike other welding processes that consume electrodes, TIG welding employs a non-consumable tungsten electrode within an inert gas shield, typically argon, to protect the weld pool from oxidation. This method makes TIG welding unparalleled in applications requiring high-quality and precise welds, such as aerospace and automotive sectors. Companies like CK World Wide have specialized equipment to support this intricate process, ensuring that professionals can work with the utmost precision and quality. The finesse required for TIG welding allows artisans to produce clean and aesthetically pleasing welds, further solidifying its reputation as a preferred method among welding experts.
Essential Tools for TIG Welding
The success of a TIG welder largely depends on the equipment used. Essential tools include a reliable TIG welder, which provides the necessary arc and heat control. A top-quality TIG torch is central to precision, and selecting the right size and type can greatly influence the quality of the weld. Additionally, support accessories such as gas lenses and a high-frequency start function can enhance performance. A dependable welding helmet is critical for protecting your eyes from harmful UV and infrared rays while offering a clear view of your work. Various brands cater to these needs, presenting options that balance safety, usability, and productivity. Efficient gas management systems also play a crucial role; optimizing the use of inert gases like argon can lead to cost savings and improved weld quality.
Mastering TIG Welding Techniques
Achieving proficiency in TIG welding techniques necessitates practice and an understanding of fundamental principles. One critical technique is mastering the torch angle; holding it at a slight angle allows the shielding gas to effectively protect the weld pool, while improper angles can lead to defects. Equally important is managing the distance between the electrode and the work piece, as this affects the weld’s penetration and width. Another integral skill is controlling the heat input, which can be adjusted by varying the welding speed. Slow speeds and high heat may lead to burn-through, while fast speeds can cause poor wetting of the metal. Incorporating filler material seamlessly involves consistent feeding and steady hand movements, contributing to a strong and uniform weld. Developing these techniques enhances overall craftsmanship, allowing welders to confidently tackle a wide range of complex projects.
Common Challenges and Solutions in TIG Welding
TIG welding, while advantageous, is not without its challenges. A frequent problem is tungsten contamination, which can arise from improper electrode preparation or contact with the weld pool. Regularly sharpening the electrode tip and maintaining cleanliness can mitigate this issue. Welders often face difficulty in maintaining the right heat input; too much can cause metal warping, while too little may result in weak joints. Adjusting settings and refining techniques are crucial in these situations. Additionally, weld bead appearance—often marred by inadequate shielding gas coverage—can be rectified by ensuring optimal gas flow rates and consistent torch positioning. Welding forums and resources like the Fabricator offer shared experiences and practical advice to help welders troubleshoot these challenges, promoting skill enhancement across the community.
Safety Protocols for TIG Welding
Ensuring safety during TIG welding is paramount. Wearing appropriate personal protective equipment (PPE) such as helmets, gloves, and aprons is essential. These items protect against UV radiation, sparks, and hot metals. A well-ventilated workspace is necessary to prevent the accumulation of harmful fumes, while fire extinguishing tools should be kept nearby as a precaution. In addition to these measures, adhering to established safety standards by organizations like OSHA helps minimize risks. Regularly inspecting equipment and maintaining a tidy workspace further mitigate hazards, empowering welders to focus on their tasks with peace of mind. By prioritizing safety, welders not only protect themselves but also ensure the longevity and reliability of their equipment and outputs.
The Benefits of TIG Welding for Various Industries
TIG welding’s benefits extend across multiple industries due to its unrivaled precision and versatility. In the aerospace sector, the ability to create high-strength, defect-free welds is crucial, especially in applications requiring complex material combinations and intricate components. Similarly, in the automotive industry, TIG welding is favored for producing strong and visually appealing joints, enhancing both functionality and aesthetics. Its application in the fabrication of thin-walled heat exchangers and custom artistic installations is also a testament to its adaptability and reliability. TIG welding ensures minimal distortion and high-quality finishes, reducing the need for extensive post-weld processing. This efficiency and cost-effectiveness are why it remains a backbone of the manufacturing sector, supporting both mass production and bespoke projects.
Conclusion
TIG welding stands out as a high-precision technique that continues to drive advancements in metal fabrication. Mastery of its tools and techniques allows welders to operate at the zenith of their craft, consistently producing results of exceptional quality. As technology evolves, staying informed about emerging trends positions professionals to adapt and innovate within the industry. By embracing the intricacies and challenges of TIG welding, practitioners enhance their skills and contribute meaningfully to the sectors they serve, ensuring their work shapes the future of metal fabrication with competence and creativity.